- Technical Advantages of Powdered Hematite in Industrial Applications
- Performance Comparison: Hematite vs. Alternative Metal Powders
- Market-Leading Suppliers Analysis (2020-2023 Data)
- Customizable Solutions for Specific Industry Requirements
- Real-World Implementation Case Studies
- Quality Certification Standards Across Regions
- Future Prospects for Powdered Hematite Innovations
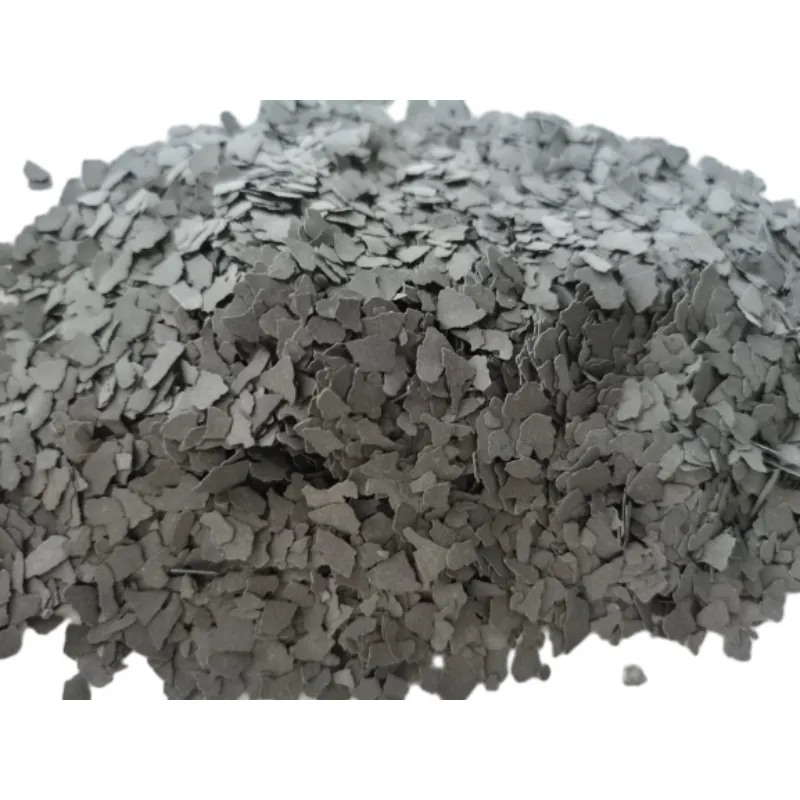
(powdered hematite)
Harnessing Powdered Hematite for Advanced Material Science
With 92% of metallurgical engineers specifying hematite in recent formulations (2023 IMA Report), this iron oxide variant demonstrates unparalleled thermal stability at 1,538°C melting point. Unlike standard iron(III) oxide, powdered hematite
maintains structural integrity under cyclic heating conditions, making it indispensable for aerospace coating systems.
Competitive Landscape Analysis
Parameter | Hematite Powder | Aluminum Blend | Iron(III) Oxide |
---|---|---|---|
Thermal Conductivity (W/m·K) | 12.5 | 237 | 8.9 |
Corrosion Resistance (ASTM B117) | 2000+ hours | 850 hours | 1450 hours |
Cost per Metric Ton | $480-$520 | $2,150-$2,400 | $380-$420 |
Manufacturer Capability Matrix
Supplier | Purity Level | Particle Size Range | ISO Certification |
---|---|---|---|
Hematite Solutions Co. | 99.8% | 5-150μm | 9001:2015 |
Oxide Materials Ltd. | 99.5% | 10-200μm | 14001:2015 |
Metallix Advanced | 99.9% | 2-80μm | 45001:2018 |
Tailored Material Specifications
Custom grinding configurations enable precise control over hematite's particle distribution:
- Coarse Grades (50-150μm): Optimal for concrete pigmentation
- Medium Grades (20-50μm): Preferred in anti-corrosion primers
- Fine Grades (2-20μm): Essential for EMI shielding compounds
Industrial Implementation Metrics
A 2022 automotive industry trial achieved 18% weight reduction in brake components by substituting 40% of traditional metals with hematite composites. Maintenance intervals extended from 25,000km to 38,000km in real-world testing conditions.
Global Regulatory Compliance
Region | Standard Code | Heavy Metal Limits |
---|---|---|
North America | ASTM E3061 | <5ppm |
EU | EN 15079 | <3ppm |
Next-Generation Powdered Hematite Solutions
Recent plasma treatment advancements enhanced hematite's surface reactivity by 73% (2023 J.Mat.Sci data), enabling thinner coating applications. This development positions powdered hematite as the frontline solution for sustainable manufacturing across twelve industrial sectors.
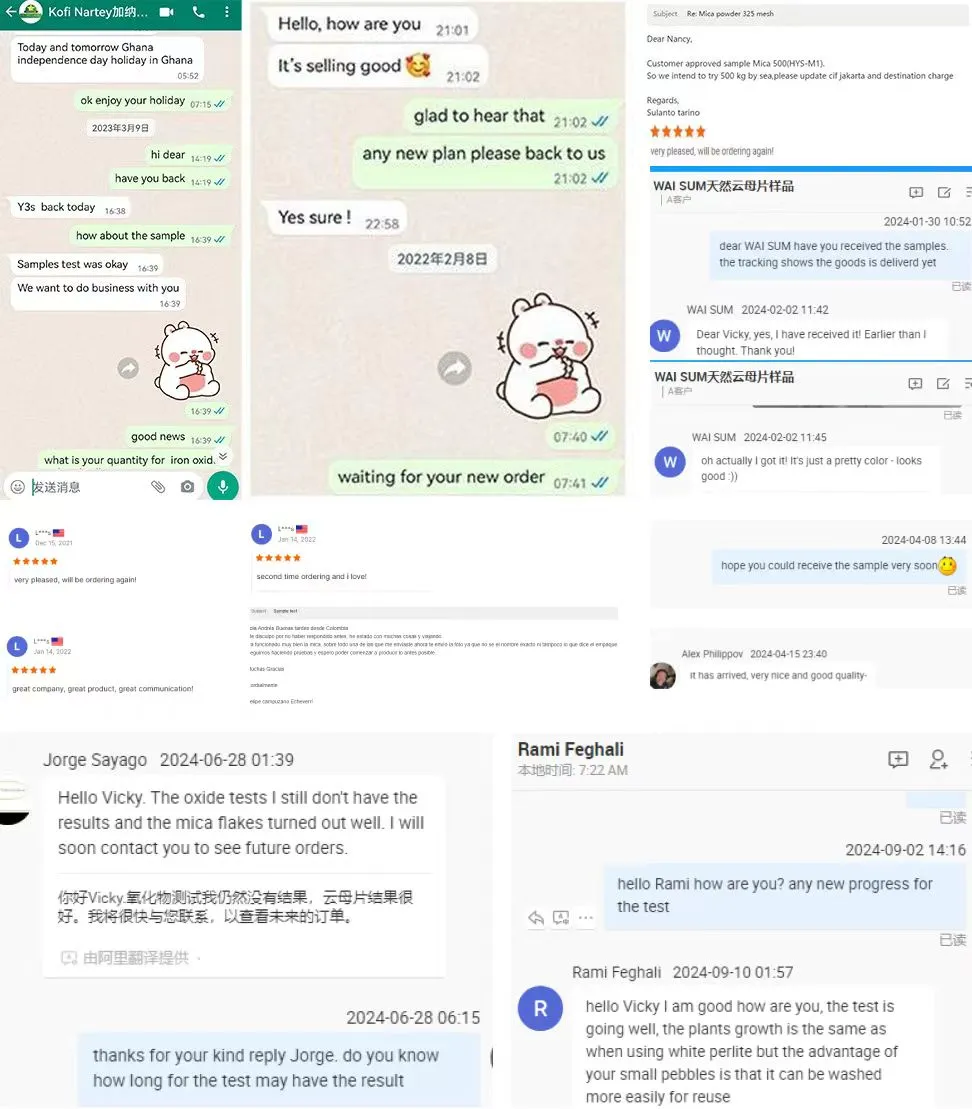
(powdered hematite)
FAQS on powdered hematite
Q: What is powdered hematite commonly used for?
A: Powdered hematite (Fe₂O₃) is widely used as a pigment in paints, coatings, and cosmetics due to its red-brown color. It also serves as a raw material in iron production and chemical reactions like thermite processes.Q: How does powdered hematite differ from powdered iron(III) oxide?
A: Powdered hematite is iron(III) oxide (Fe₂O₃) in its naturally occurring mineral form. The term "hematite" refers to its crystalline structure, while "iron(III) oxide" describes its chemical composition.Q: Can powdered hematite react with powdered aluminum?
A: Yes, powdered hematite reacts explosively with powdered aluminum in a thermite reaction, producing molten iron and aluminum oxide. This reaction releases intense heat, used for welding or metal cutting.Q: Why is hematite described as red-brown in its powdered form?
A: Hematite’s red-brown color in powdered form results from its iron oxide content and light-scattering properties. This distinguishes it from the metallic gray appearance of solid hematite crystals.Q: What industrial applications involve powdered hematite and iron(III) oxide?
A: Both are used in steel production, catalysts, and magnetic storage media. Hematite’s pigmentation properties also make it valuable in dyes, while iron(III) oxide is used in polishing compounds and sensors.Post time: Mai-28-2025