- Introduction to Ceramic Media Balls: Definition and Core Properties
- Key Technical Advantages of Ceramic Media Balls
- Manufacturer Comparison: Global & Chinese Ceramic Balls Vendors
- Custom Solutions: Sizing, Composition, and Performance Tailoring
- Industry Applications and Use Cases
- Data Analysis: Performance Table of Ceramic, Silicon Nitride & Chinese Balls
- Conclusion: Ceramic Media Balls in Advanced Industrial Use
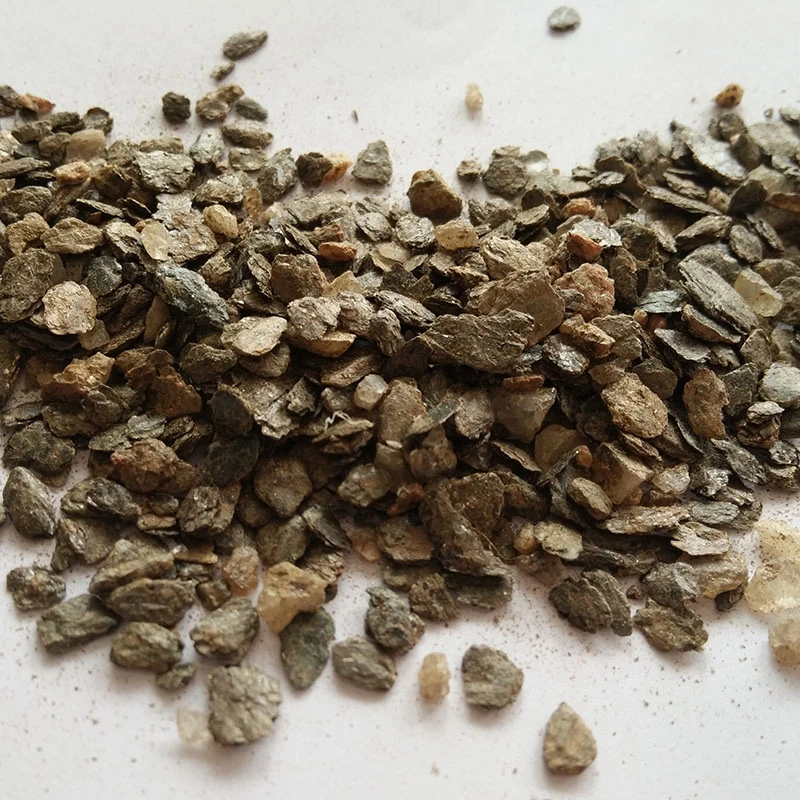
(ceramic media balls)
Introduction to Ceramic Media Balls: Properties, Usage, and Technology
Ceramic media balls are high-performance, precision-engineered spheres made from advanced ceramic materials, commonly employed in high-intensity environments where exceptional hardness, corrosion resistance, and dimensional stability are required. These components are distinct from conventional metal or polymer balls, owing to their inherent structural stability, low density, and unique thermal characteristics. Their core applications span across sectors such as mechanical engineering, energy, chemical processing, mining, and precision bearings, reflecting their versatility and indispensability.
Ceramic media balls are available in a diverse range of compositions, including zirconia, alumina, and the highly sought-after silicon nitride. Demand for these materials is projected to witness a 6.2% CAGR through 2030, with the Asia-Pacific region – particularly China – playing a pivotal role in both production and application. Unlike metallic alternatives, ceramic balls exhibit minimal wear, offer non-magnetic properties, and retain performance across a vast temperature spectrum, with some grades operating reliably up to 1400°C. Their adoption is accelerating, with over 430 million units estimated for use globally in 2023.
Technical Superiority: Why Ceramic Media Balls Stand Out
The superiority of ceramic media balls
lies in a set of tangible, quantifiable metrics. Silicon nitride ceramic balls, in particular, exhibit a Vickers hardness exceeding 1,650 HV, density as low as 3.2 g/cm3, and compressed modulus values upwards of 310 GPa. These technical parameters translate to several operational advantages: extended service lifespan, lower maintenance requirements, enhanced running speeds, and reduced system contamination risks. Their low weight further permits energy savings in rotational applications and yields a lower centrifugal force, minimizing wear on supporting components.
Chemically, advanced ceramics are inert to most acids and alkalis, making them suitable for aggressive environments such as slurry pumps, fluid mixers, and grinding mills. Electrically, their high resistivity brings utility in electronic and semiconductor manufacturing sectors, where cleanliness and non-conductivity are paramount. When compared to chrome or stainless steel equivalents, the wear rate of ceramic media balls is typically 10x lower, especially in abrasive or corrosive media.
Manufacturer Landscape: Global and Chinese Vendors of Ceramic Media Balls
The manufacturing ecosystem for ceramic media balls is led by a mix of established international brands—such as Toshiba Materials, Saint-Gobain, and CoorsTek—and a rapidly emerging cluster of Chinese ceramic ball producers, including Sinoma, Jingang New Materials, and Zibo Saina New Material Technology. Global suppliers often focus on specialized grades and tight tolerance controls, while Chinese ceramic balls have made exceptional headway in mass-market and mid-tier product segments, driving volume scalability and cost effectiveness.
Over 60% of global production now originates from mainland China, with continuous investment in automated precision forming, high-temperature sintering, and advanced surface finishing. Price benchmarking suggests that Chinese ceramic balls can deliver up to 25-30% cost savings over equivalents from Western suppliers, with quality metrics converging annually as Chinese vendors invest in R&D and quality systems.
Custom Solutions: Tailoring Composition, Size, and Performance Parameters
The evolving needs of end-users have fostered a marketplace where customization is not merely an advantage but a critical requirement. Suppliers routinely offer ceramic media balls in diameter ranges spanning 0.5 mm to over 60 mm, with roundness tolerances as fine as 0.01 mm. Users in industries such as aerospace and dental tools may request hybrid solutions combining core ceramics with specific metallic coatings to leverage unique thermal or tribological properties.
Composition variation is another driver; while pure alumina and silicon nitride dominate, emerging demand for yttria-stabilized zirconia and silicon carbide media balls is evident in ultra-high wear environments. Doping, surface texturing, and even colored identifiers are additional customizable parameters, enabling quick identification and process optimization in high-mix manufacturing settings. Manufacturers deploy both batch and continuous kiln sintering processes to ensure consistent grain structures and performance characteristics, supporting 24/7 operation cycles and rapid changeover in OEM lines.
Industry Adoption: Application Cases from Global Sectors
Ceramic media balls play a transformative role across multiple industries. In mining and mineral processing, wear-resistant balls have driven a 35% increase in asset uptime, drastically reducing mill maintenance frequency. Semiconductor tool manufacturers rely on silicon nitride ceramic balls for their superior cleanliness and non-magnetic properties, supporting process nodes as small as 3 nm. In the automotive sector, hybrid bearings containing ceramic balls extend electric vehicle (EV) drive unit life by up to 70%, while thermal stability assures consistent performance in high-speed applications exceeding 50,000 rpm.
Other compelling cases include pharmaceutical batch grinding, where chemical inertness prevents contamination and color transfer, and chemical reactors, where increased hardness and density ensure critical operation even under highly acidic or basic environments. Custom Chinese ceramic balls have penetrated global supply chains for wind turbine pitch systems, aerospace compressors, and food-grade grinding, resulting in lower operational costs and longer component reliability windows.
Performance Comparison: Ceramic, Silicon Nitride, and Chinese Ceramic Balls
Parameter | Alumina Ceramic Balls | Silicon Nitride Ceramic Balls | Chinese Ceramic Balls |
---|---|---|---|
Hardness (Vickers, HV) | 1,200 - 1,500 | 1,600 - 1,750 | 1,100 - 1,450 |
Density (g/cm3) | 3.65 - 3.9 | 3.20 - 3.30 | 3.35 - 3.85 |
Max Working Temp (°C) | 1,000 | 1,200 - 1,400 | 900 - 1,100 |
Compressive Strength (MPa) | 2,300 | 3,700 | 2,000 - 2,800 |
Wear Loss (mg/100 hrs/80N) | 9 - 11 | 1 - 2 | 5 - 12 |
Average Lead Time (days) | 30-45 | 60-80 | 14-30 |
Unit Price Index (%) | 100 | 145 | 70 |
Common Applications | Milling, Filtration, Bearings | High-Precision Bearings, Electronics, Aerospace | Mining, Bulk Grinding, General Industrial |
Conclusion: Ceramic Media Balls as Industrial Game Changers
In an intensely competitive, data-driven industrial world, ceramic media balls have firmly positioned themselves as indispensable for modern processing, grinding, and rotational systems. Combining unrivaled mechanical properties, chemical resilience, and energy-saving advantages, their value proposition is further enhanced by aggressive innovation among both traditional global manufacturers and high-output Chinese ceramic balls suppliers. The progressive shift toward application-specific, custom-engineered media is set to redefine what is possible in operational efficiency, uptime, and component longevity throughout an expanding array of sectors. As technological demands in precision industries continue to climb, ceramic media balls remain at the forefront, catalyzing improvements and shaping the future of advanced manufacturing routines.
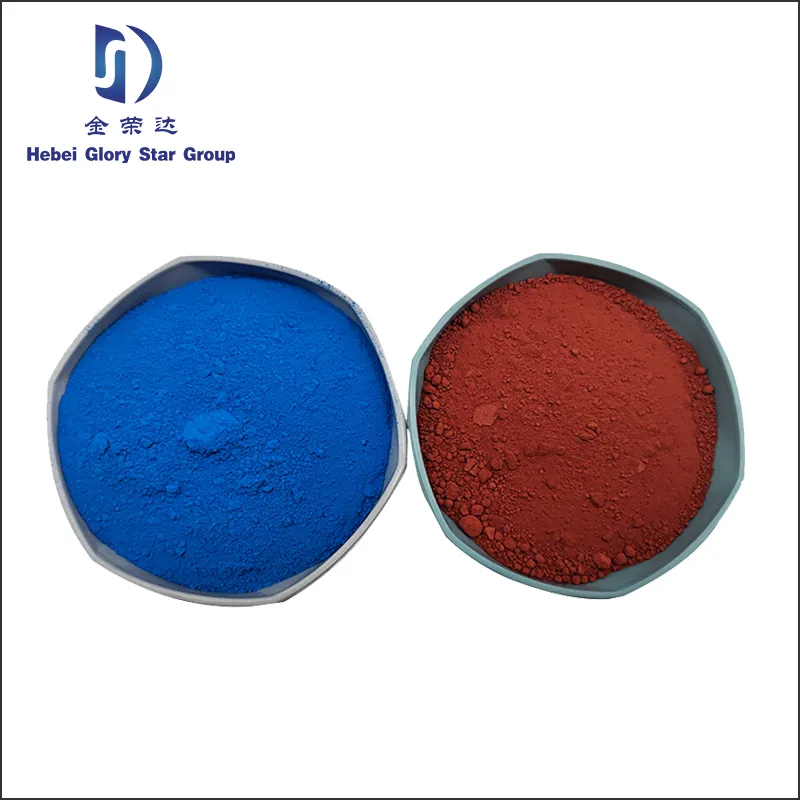
(ceramic media balls)
FAQS on ceramic media balls
Q: What are ceramic media balls used for?
A: Ceramic media balls are primarily used for grinding, mixing, and dispersing materials in industrial processes. They offer high hardness, wear resistance, and excellent chemical stability. Common applications include ball milling and filtration.Q: What advantages do silicon nitride ceramic balls have over standard ceramic media?
A: Silicon nitride ceramic balls provide superior strength, lighter weight, and greater resistance to heat. They are ideal for high-speed and precision applications. Their durability makes them popular in bearings and demanding environments.Q: Are Chinese ceramic balls reliable for industrial applications?
A: Yes, many Chinese ceramic ball manufacturers offer products that meet international quality standards. Chinese ceramic balls are widely used globally due to their cost-effectiveness and consistent performance. Always check supplier certifications for assurance.Q: How do ceramic media balls differ from steel grinding balls?
A: Ceramic media balls are non-metallic, chemically inert, and much harder than steel balls. They minimize contamination in grinding processes and last longer in corrosive environments. Steel balls, however, are sometimes preferred for cost reasons.Q: Can silicon nitride ceramic balls be used in high-temperature environments?
A: Yes, silicon nitride ceramic balls can withstand very high temperatures without degrading. Their thermal stability makes them suitable for aerospace, automotive, and industrial applications. They maintain performance even under extreme heat.Post time: జూలై-07-2025