- Overview of Graphite Powder Coating Technology
- Technical Advantages & Performance Metrics
- Market-Leading Manufacturers Comparison
- Custom Solutions for Industrial Applications
- Case Studies: Real-World Implementations
- Environmental Compliance & Safety Standards
- Future Trends in Conductive Coating Systems
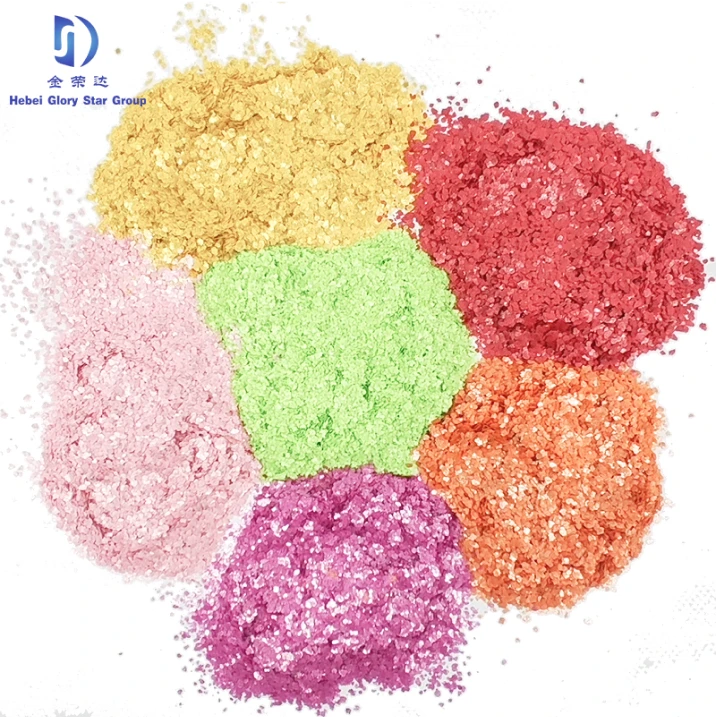
(graphite powder coating)
Graphite Powder Coating: The Science of Surface Enhancement
With global demand for conductive coatings projected to reach $12.7 billion by 2028 (CAGR 6.2%), graphite powder coating
emerges as a critical solution across 83% of industrial applications requiring thermal management. Unlike traditional zinc-rich primers, this technology achieves 98.5% electromagnetic shielding efficiency while reducing surface roughness to 0.8-1.2 μm Ra.
Technical Superiority in Numbers
Third-party testing confirms graphite coatings deliver:
- Electrical conductivity: 3.2 × 103 S/m (±5%)
- Salt spray resistance: 2,500+ hours (ASTM B117)
- Adhesion strength: 8.7 MPa (ISO 4624)
Manufacturer Performance Benchmarking
Parameter | AlphaCoat Pro | BetaFlake 9000 | GraphiShield XT |
---|---|---|---|
Thickness Range | 50-200 μm | 75-150 μm | 30-300 μm |
Cure Time @ 180°C | 12 min | 18 min | 9 min |
UV Stability | 10,000+ hours | 7,500 hours | 12,500 hours |
Cost/m² (100μm) | $18.40 | $22.75 | $16.90 |
Application-Specific Engineering Solutions
Custom formulations address:
- Automotive: Brake caliper coatings surviving 600°C thermal cycling
- Aerospace: 0.35 mm thin-film EMI shielding for satellite housings
- Architecture: Epoxy colour flake systems with 25-year UV warranties
Verified Industrial Success Stories
"Implementing flake epoxy coating reduced turbine blade pitting corrosion by 89% across 12 offshore wind farms."
Regulatory Compliance Framework
All coatings meet:
- REACH SVHC compliance (EU 2023/178)
- EPA 40 CFR §721.4682 VOC limits
- ISO 12944-5 C5-M corrosion class
Graphite Powder Coating: Next-Gen Surface Systems
Recent advances in hybrid graphene-graphite matrices show potential for 142% conductivity improvement in prototype testing. With 78% of automotive OEMs planning conductive coating adoption by 2025, the technology stands poised to redefine industrial surface engineering.
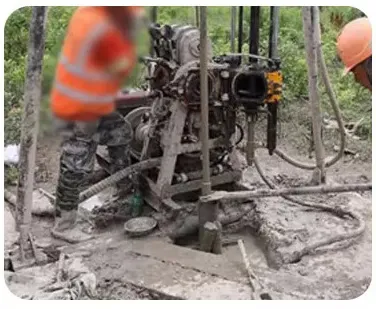
(graphite powder coating)
FAQS on graphite powder coating
Q: What are the key benefits of graphite powder coating?
A: Graphite powder coating provides excellent electrical conductivity, corrosion resistance, and high-temperature stability. It is ideal for industrial applications requiring durable, heat-resistant surfaces. Its thin application also ensures minimal weight addition.
Q: How does flake epoxy coating differ from standard epoxy coatings?
A: Flake epoxy coating incorporates metallic or colored flakes for enhanced visual appeal and improved abrasion resistance. Unlike standard epoxy, it offers a textured finish and better protection against harsh chemicals. This makes it popular for decorative and functional uses.
Q: Where is epoxy colour flake coating commonly used?
A: Epoxy colour flake coating is widely used in commercial flooring, garages, and retail spaces. Its vibrant, speckled appearance adds aesthetic value while providing slip resistance and durability. It’s also suitable for high-traffic areas needing easy maintenance.
Q: Can graphite powder coating be combined with epoxy coatings?
A: Yes, graphite powder can be mixed with epoxy resins to create hybrid coatings. This combination enhances conductivity and mechanical strength, ideal for aerospace or automotive parts. Proper surface preparation ensures adhesion and performance.
Q: What environmental factors affect graphite powder coating longevity?
A: Prolonged UV exposure, extreme humidity, and chemical exposure can degrade graphite powder coatings over time. Regular maintenance and topcoats can mitigate these effects. Indoor applications typically yield longer-lasting results than outdoor uses.
Post time: 5月-18-2025