- Introduction to iron oxide and its industrial importance
- Types of iron oxide and their properties
- Extraction of iron from iron oxide: Processes and advancements
- Technical advantages and challenges in iron and iron oxide applications
- Industry vendor comparison and tabulated data analysis
- Custom solutions for iron iron oxide utilization across sectors
- Conclusion: Iron oxide is a strategic material for modern industries
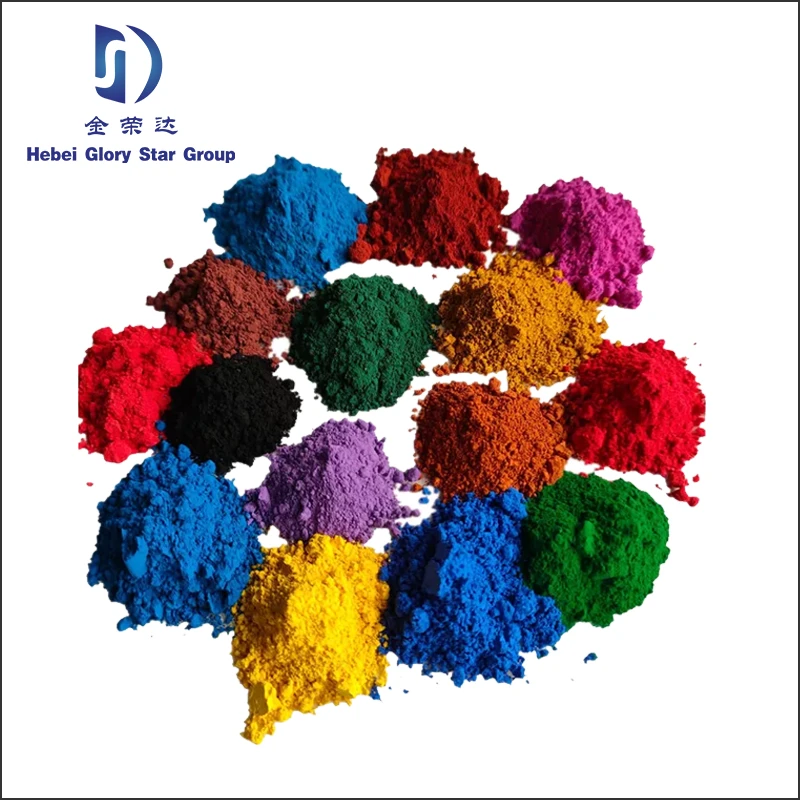
(iron oxide is a)
Iron oxide is a Cornerstone of Industrial Progress
Iron oxide is a material of profound industrial significance, contributing considerably to global production processes. From pigment manufacturing and steelmaking to advanced catalysis in environmental technologies, its versatility stands unrivaled. Recent data estimates that over 120 million metric tons of iron oxide pigments are utilized annually, with the market projected to grow at a Compound Annual Growth Rate (CAGR) of 4.5% through 2030.
This robust demand is underpinned by iron oxide’s role in producing pure iron, sparking advances in fields ranging from construction to electronics. As industries transform to accommodate stricter environmental standards and seek sustainable raw materials, the functional and strategic value of iron oxide is more pronounced than ever before.
Variants and Unique Properties of Iron Oxide
Naturally occurring iron oxides are primarily classified into hematite (Fe2O3), magnetite (Fe3O4), and goethite (FeO(OH)). Each variant serves distinct industrial functions:
- Hematite: Offers a high iron content with superior corrosion resistance. Widely exploited in steel manufacturing, hematite ensures durability and structural integrity.
- Magnetite: Noted for its magnetic properties, it is essential in magnetic separation technologies, water purification, and as black pigment in plastics and paints.
- Goethite: Valued for its brownish-yellow hue and reactive surface, making it ideal for catalysis and adsorption applications.
Iron from Iron Oxide: Extraction Processes and Innovation
Decades of scientific endeavor have refined the mechanisms for extracting iron from iron oxide. The classic blast furnace process remains prevalent, leveraging the reduction of iron oxide using coke to yield molten iron and carbon dioxide. However, with rising sustainability demands, alternative solutions like direct reduced iron (DRI) and hydrogen-based reduction are gaining traction.
- Direct Reduction: Involves reducing iron oxide at lower temperatures using natural gas, cutting CO2 emissions by up to 60% compared to traditional routes.
- Hydrogen Reduction: Emerging pilot plants in Europe showcase reductions in greenhouse gas emissions of over 90%, setting benchmarks for decarbonized steel production.
Technical Advantages and Cross-Sector Challenges
The application ecosystem for both iron and iron oxide extends from structural steel and catalysts to pigmentation and environmental filters. Engineered iron oxide particles demonstrate high surface area and chemical tunability, leading to improved adsorption efficiencies—documented at removal rates up to 98% for heavy metal ion cleanup in wastewater.
However, challenges persist:
- Heat Stability: While iron oxide maintains stability up to 850°C, certain applications demand higher resistance, prompting exploration of composite materials.
- Agglomeration: Nanostructured iron oxide particles can clump, potentially reducing reactivity. Advances in surface engineering and particle coating are addressing these limitations for next-generation products.
Industry Leaders: Vendor Comparison Table
When considering procurement or integration of iron oxide products, understanding vendor capabilities is crucial. The following table compares key manufacturers based on market presence, production volume, range, and customization prowess:
Vendor | Global Market Share (%) | Annual Production (kTons) | Product Range | Customization Capacity | Lead Time (Weeks) |
---|---|---|---|---|---|
BASF | 23 | 180 | Fe2O3, Fe3O4, Pigments | High | 3–5 |
Lanxess | 17 | 135 | Hematite, Magnetite, Blends | Medium | 4–7 |
Venator | 12 | 90 | Pigments, Specialty Grades | Very High | 2–4 |
Alfa Aesar | 5 | 15 | High-Purity, Nano Iron Oxide | Custom R&D | 6–8 |
This vendor landscape highlights significant disparities in customization and production scale, steering procurement decisions for niche as well as bulk-use requirements.
Tailored Solutions for Iron Iron Oxide Applications
The diversity of sectors utilizing iron iron oxide has prompted manufacturers to develop highly tailored solutions:
- Construction: Customized pigment blends for concrete offer enhanced weathering properties and desired aesthetic shades for mega infrastructure projects.
- Environmental Remediation: Engineered nano iron oxide is functionalized to target specific contaminants, facilitating sustainable groundwater and soil remediation.
- Advanced Electronics: Ultra-fine magnetite enables sensitive magnetic sensors and shielding in electronic assemblies.
Case studies show that custom iron oxide blends can increase pigment dispersibility by up to 27% in polymer resins, or cut operating costs in water treatment by 15–22% compared to generic alternatives.
Conclusion: Iron oxide is a Strategic Driver of Sustainable Industry
As a unifying resource bridging the elemental gap between iron, iron oxide, and engineered materials, iron oxide is a
pivotal driver of both industrial output and innovation. Whether serving as a direct precursor to high-purity iron, a performance pigment, or a transformative catalyst, its value chain amplifies both economic efficiency and sustainability.
With ongoing advances in extraction, purification, and application engineering, iron from iron oxide continues to unlock possibilities across the built environment, clean technologies, and advanced manufacturing. Strategic sourcing and co-development partnerships will accelerate these gains—anchoring iron oxide’s role as an indispensable, forward-looking material for generations to come.
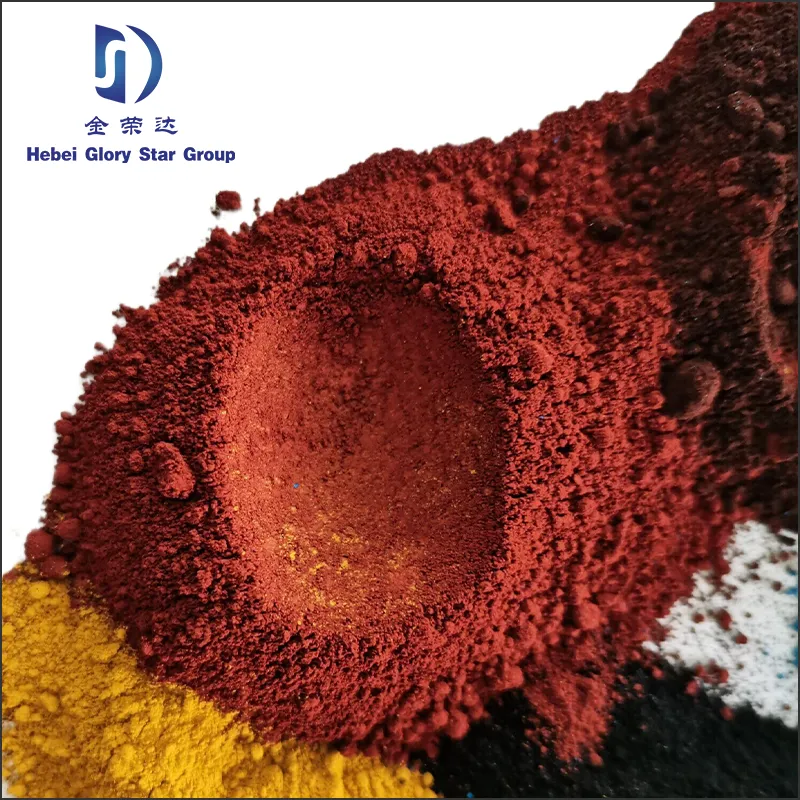
(iron oxide is a)
FAQS on iron oxide is a
Q: What is iron oxide?
A: Iron oxide is a chemical compound made from iron and oxygen. It occurs naturally as minerals like hematite and magnetite. It is commonly seen as rust.Q: How is iron obtained from iron oxide?
A: Iron can be extracted from iron oxide through a reduction process, often using a blast furnace. Carbon (in the form of coke) reduces iron oxide to iron and carbon dioxide. This is a key step in steel production.Q: What is the difference between iron and iron oxide?
A: Iron is a metallic element (Fe), while iron oxide is a compound of iron and oxygen. Iron oxide comes in various forms, such as FeO and Fe2O3. The properties of iron oxide differ significantly from pure iron.Q: Can iron form oxides with different compositions?
A: Yes, iron can form several oxides, including FeO, Fe2O3, and Fe3O4. The number of oxygen atoms varies in each compound. These oxides have unique chemical and physical properties.Q: Is there a relationship between iron, iron oxide, and rust?
A: Yes, rust is primarily composed of iron oxides that form when iron reacts with oxygen and moisture. Iron and iron oxide are chemically related through this oxidation process. Preventing rust involves protecting iron from exposure to air and water.Post time: Jun-24-2025