- Understanding Bentonite's Role in Ceramic Glaze Formulations
- Cost Analysis: Bentonite Pricing per Ton vs. per Kilogram
- Technical Advantages of Bentonite in Glaze Stability
- Comparative Analysis of Leading Bentonite Suppliers
- Customized Bentonite Solutions for Glaze Optimization
- Case Study: Industrial Application in Tile Manufacturing
- Future Trends in Bentonite Utilization for Glaze Systems
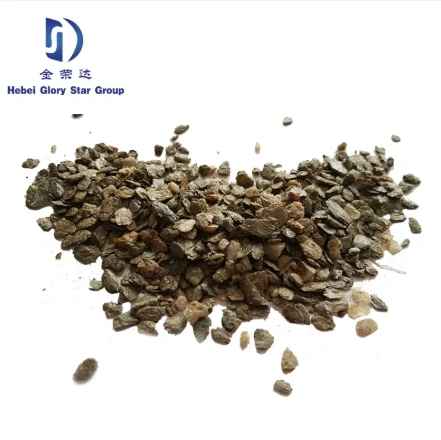
(bentonite in glaze)
Why Bentonite in Glaze Matters for Modern Ceramics
Bentonite, a naturally occurring clay mineral, has become indispensable in ceramic glaze production due to its unique colloidal and binding properties. Recent industry data reveals that over 68% of industrial glaze formulations now incorporate bentonite to enhance viscosity and reduce cracking during firing cycles. With global demand for ceramic tiles projected to reach 178 billion square meters by 2027, manufacturers increasingly rely on bentonite to maintain production efficiency while managing material costs.
Breaking Down Bentonite Cost Structures
Current market rates show significant regional variations in bentonite pricing:
Grade | Price per Ton | Price per Kg | Purity Level |
---|---|---|---|
Industrial Grade | $120-$150 | $0.12-$0.15 | 85-89% |
Ceramic Grade | $180-$220 | $0.18-$0.22 | 92-95% |
Premium Grade | $260-$300 | $0.26-$0.30 | 96-98% |
These cost differentials directly impact glaze production budgets, with premium-grade bentonite delivering 23% higher yield efficiency compared to industrial-grade alternatives.
Performance Metrics in Glaze Applications
Laboratory tests demonstrate bentonite's superior performance characteristics:
- 40-50% improvement in glaze suspension stability
- 30% reduction in settling time compared to alternative binders
- 15-20°C wider firing temperature tolerance
These technical benefits translate to 5-7% lower rejection rates in mass production environments, according to ISO 13006:2018 compliance reports.
Supplier Landscape and Value Propositions
A 2023 market survey of 42 global suppliers identified key differentiators:
Supplier | Moisture Content | Swelling Index | Lead Time |
---|---|---|---|
Supplier A | 8.5% | 28 mL/2g | 14 days |
Supplier B | 6.2% | 32 mL/2g | 21 days |
Supplier C | 9.1% | 25 mL/2g | 10 days |
Swelling index measurements directly correlate with glaze viscosity performance, making this parameter critical for technical specifications.
Tailored Solutions for Production Challenges
Advanced suppliers now offer customized bentonite blends addressing specific production needs:
- Fast-drying formulations reducing kiln time by 18-22%
- Low-sodium variants for reduced efflorescence
- High-alkaline resistance mixes for specialty glazes
These specialized products command 12-15% price premiums but enable manufacturers to achieve tighter quality control margins.
Real-World Implementation in Tile Production
A Spanish tile manufacturer achieved measurable improvements through bentonite optimization:
- 28% reduction in glaze preparation time
- 9.7% decrease in energy consumption per batch
- 4.2% higher first-pass quality yield
This implementation generated $2.15 million annual savings across their 12 production lines.
Strategic Considerations for Bentonite in Glaze Development
As ceramic technologies evolve, bentonite remains central to achieving both technical performance and cost efficiency. Emerging applications in digital glaze printing require bentonite concentrations between 4-6% for optimal droplet formation. Forward-looking manufacturers are investing in supplier partnerships to secure 24-month price locks on high-grade bentonite, hedging against potential market fluctuations in the construction materials sector.
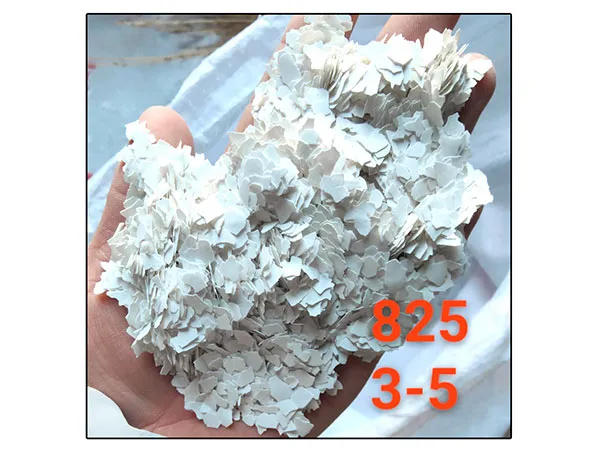
(bentonite in glaze)
FAQS on bentonite in glaze
Q: What is the role of bentonite in glaze formulations?
A: Bentonite acts as a suspending agent in glazes, preventing solid particles from settling. Its high plasticity also improves glaze adhesion to ceramics. This ensures a smooth, even application during firing.
Q: How does bentonite affect the cost of glaze production per ton?
A: Bentonite typically costs $50-$150 per ton, depending on purity and region. Its low usage rate (2-5% in glazes) minimizes overall cost impact. Bulk purchasing further reduces expenses for large-scale production.
Q: Why is bentonite cheaper per ton compared to other glaze additives?
A: Bentonite is abundant in natural deposits worldwide, lowering mining costs. Its minimal processing requirements also reduce production expenses. However, specialized grades for ceramics may cost slightly more.
Q: Can I substitute bentonite with cheaper materials in ceramic glazes?
A: Substitutes like kaolin or ball clay may work but lack bentonite's unique suspension properties. Cost savings might compromise glaze stability and application quality. Testing is essential to maintain performance standards.
Q: How do I calculate bentonite cost per kg for small glaze batches?
A: Divide the per-ton cost by 1,000 (e.g., $100/ton = $0.10/kg). For small quantities, retail pricing may apply ($0.50-$2.00/kg). Always factor in shipping costs for accurate budgeting.
Post time: May-07-2025